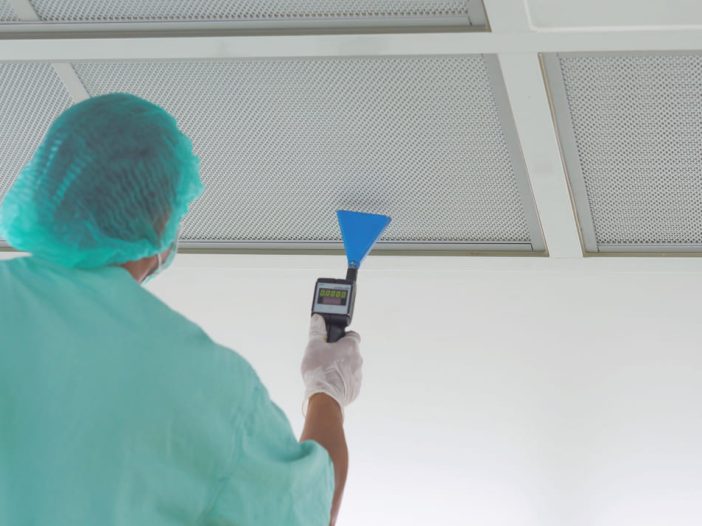
In molte filiere di produzione industriale (alimentare, farmaceutica, elettronica) esiste un rischio di contaminazione dei prodotti dovuta a polvere, muffa e particelle che andrebbe a ridurre la qualità degli stessi. Diventa quindi un requisito essenziale applicare procedure di “protezione del prodotto” dai danni che possono essere causati dalla contaminazione di particelle inerti o di microrganismi (o altri minuscoli organismi) presenti nell’aria. In questi processi, quindi, le fasi più delicate della lavorazione vengono effettuate in specifici ambienti realizzati in modo da minimizzare l‘introduzione e la ritenzione di particelle inquinanti al loro interno: le “camere bianche” o clean rooms.
Per definizione, una “camera bianca” è un locale nel quale viene controllata la concentrazione delle particelle trasportate [veicolate, disperse, diffuse, trasportate passivamente] dall’aria. La progettazione e il funzionamento fanno riferimento alle norme della serie ISO 14644 e agli Standard internazionali di “Clean rooms and associated controlled environments” che si concentrano su tutti gli aspetti critici per il raggiungimento dell’obiettivo. Tali norme intervengono su tutte le fasi che riguardano una camera bianca, dalla classificazione alle caratteristiche, dalla progettazione alla costruzione, dal collaudo al loro funzionamento a regime, dai comportamenti del personale che vi lavora alle metodiche di pulizia e disinfezione.
Lo status di “camera bianca” viene raggiunto e mantenuto attraverso il filtraggio dell’aria atmosferica (in modo da ottenere la classe di pulizia necessaria a evitare la contaminazione e gestire i parametri ambientali di temperatura e umidità) e da un regime di sovrapressione interna costante, così da realizzare le condizioni di lavoro e di processo necessarie e richieste.
La circolazione dell’aria in questi locali è pertanto forzata. In entrata sono presenti i cosiddetti “filtri assoluti” rappresentati dai filtri hepa e dai più potenti filtri ulpa con un’efficienza di filtrazione fino al 99,999995% di particelle. L’aria viene immessa attraverso il soffitto e aspirata dal pavimento e non deve avere un movimento turbolento. Sofisticati sistemi di misurazione computerizzati aiutano nella gestione di questi processi e, anche grazie a una serie di sistemi di allarme, permettono che il sistema sia costantemente tenuto sotto controllo.
Un importante fattore di rischio è legato alla presenza di persone e al trasferimento di materiali, che dovranno essere gestiti in un’ottica complessiva della lavorazione, individuando delle “zone grigie” di avvicinamento e preparazione alla “camera bianca”.
In queste delicate filiere di produzione, naturalmente, esiste anche un rischio legato alla presenza di infestanti (artropodi e roditori) che non può essere sottovalutato.
L’attenzione deve essere posta principalmente alle zone grigie esterne alla camera bianca (nella quale, grazie alle azioni applicate esternamente a essa, non si deve mai e comunque manifestare l’infestazione) e particolarmente nelle altre restanti aree del sito. Qui, dopo un’accurata analisi dei punti critici, deve essere impostato un attento piano di prevenzione e monitoraggio di quegli infestanti potenzialmente presenti (in primis blatte e roditori, ma anche altri insetti volanti o striscianti) in modo che, in caso di “non conformità” sia possibile effettuare trattamenti rapidi e puntuali prima che la situazione possa degenerare.